Questi mesi del 2020 corrispondono ad un momento storico in cui c’è bisogno di belle storie e di ottimismo. Per questo vi vogliamo raccontare come i legami tra le persone della nostra azienda e le realtà produttive del territorio, ci abbiano regalato la possibilità di fare qualcosa di utile.
L’idea iniziale era di fare la propria parte e contribuire alla produzione di respiratori per persone affette da problemi respiratori, partendo dalle maschere da snorkeling in commercio, sulla base dall’intuizione del Dott. Renato Favero poi realizzata da Isinnova per le maschere della Decathlon. Nel realizzare questo, quasi senza rendercene conto, si è creata sotto ai nostri occhi una Smart Factory, che seppur frammentata a livello geografico è riuscita a lavorare a livello industriale in modo organizzato, unita dal comune obiettivo di essere d’aiuto alla comunità.
Ecco come è nata l’idea e quali sono le difficoltà e le fasi che hanno portato alla sua realizzazione.
Indice dei prodotti di stampa:
Come è nato il progetto
Marco Martelli, responsabile della divisione additive Manufacturing di Nuovamacut, spiega la genesi del progetto:
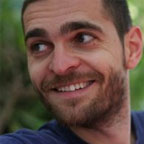
“Mi sono imbattuto su un post su LinkedIn di un mio contatto che parlava di un’idea di un medico in pensione, il Dott. Renato Favero, che aveva intuito come ci fosse una grande somiglianza tra i dispositivi utilizzati in terapia intensiva per l’ossigenazione forzata dei pazienti e le maschere da snorkeling della Decathlon. Il medico aveva contattato Isinnova, una società bresciana che pochi giorni prima aveva reingegnerizzato e prodotto con una stampante 3D una valvola venturi di un casco CPAP. Da lì era nato un collettore per trasformare le maschere Decathlon in un respiratore per terapia intensiva e sub-intensiva. Ci sono altri produttori di quel tipo di maschere, così ne ho ordinata una online e nel mentre ho scritto ad un mio collega Michele Sambo, appassionato di subacquea, per capire se avesse contatti con qualche produttore”
- Lo studio del prototipo di connettore sarebbe stato fortemente limitato dagli strumenti presenti in casa: a disposizione solo un calibro e tanta buona volontà.
- Una volta realizzato il prototipo e messo a disposizione della community di makers, questi avrebbero poi trovato una reale disponibilità delle maschere nei magazzini e nei negozi, dato il blocco della produzione in questo momento storico particolare?
- Chi avrebbe distribuito questo prototipo? Avevamo un contatto con un solo distributore e non sapevamo come gestire a livello di logistica la consegna delle mascherine agli ospedali.
L’obiettivo era mettere a disposizione degli ospedali dei respiratori in modo veloce, serviva un approccio più efficace.
Approccio Industriale
E’ stato scelto di adottare un approccio industriale, per riuscire a:
- bypassare le tempistiche richieste dall’attività di reverse engineering della maschera ordinata online, arrivando al risultato in tempi più veloci;
- mettere in relazione l’esperienza e la competenza dei produttori di maschere con la conoscenza in materia di modellazione della community di clienti HP, così da utilizzare come volano la contaminazione tra eccellenze in campi specifici per raggiungere il migliore risultato possibile;
- affidare la logistica direttamente ai produttori, appoggiandosi ad un sistema già esistente e quindi attivabile in modo efficace e rapido.
Dopo aver parlato con Marco Martelli, Michele Sambo, Delivery and Presales Manager di Nuovamacut, tramite una serie di contatti personali è quindi riuscito a contattare la Mares, nota azienda ligure produttrice di attrezzatura per le immersioni.
Dallo scambio telefonico con il CTO di Mares, Sergio Angelini, è nata l’intesa e il nostro team è stato indirizzato verso il senior R&D Engineer di Mares, che proprio in quei giorni stava lavorando su un modello di adattatore capace di rendere la maschera un respiratore.
Sergio Angelini, CTO Mares
La collaborazione con Mares e con le aziende del nostro network
La matematica del progetto era quasi pronta, ma restava l’ostacolo del produrre il pezzo in 3D.
Mares ha realizzato fisicamente il progetto del connettore e ci ha fatto avere il file che abbiamo a nostra volta inviato ad un nostro cliente, Mira Meccanica, che si era reso disponibile a realizzare i primi prototipi funzionali in varie forme e versioni con una stampante HP Multi Jet Fusion 580, utilizzando il materiale PA12.
Oltre a Mira Meccanica si sono rese disponibili a stampare nel giro di pochi giorni anche Protoflash, Pariani, FPZ, PIUSI, Campetella Robotics Center, Ferrari, Everex, Juno Design, SB3 e Innovamec. Siamo così riusciti a produrre più di 1.200 collettori e quasi 1.000 maschere assemblate e consegnate a tantissimi ospedali in tutta Italia (Parma, Bologna, Imola, La Spezia, Genova, Rapallo, Brescia, Pinerolo e tanti altri).
Michele Sambo riporta la sua impressione personale:
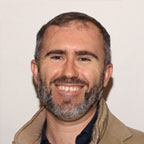
“L’aspetto, a mio vedere, eccezionale è stato il tempismo con cui sono avvenuti i contatti, l’espressione “allineamento dei pianeti” descrive perfettamente la sincronia di orbite e tempi completamente diversi che in quel preciso momento si sono allineati. Un altro aspetto che ha reso tutto questo possibile è stata sicuramente la passione, l’entusiasmo, la determinazione, la professionalità e la capacità di gettare il cuore oltre l’ostacolo da parte di tutte le persone coinvolte, unico obiettivo quello di dare una mano alla situazione contingente. Sembrava che ci conoscessimo tutti da tempo, che ci fosse già un’organizzazione alle spalle ben oliata. Ed era la prima volta che accadeva. Credo che questo sia potuto accadere perché tutti avevamo un medesimo obiettivo -provare a fare del bene in modo disinteressato- e le stesse priorità.”
Marco Martelli insiste nel sottolineare come l’intuizione del Dott. Renato Favero e la realizzazione da parte di Innova, siano state le fonti d’ispirazione più importanti per questo progetto e sottolinea:
“Questa è l’ennesima conferma di come la stampa 3D sia un strumento potentissimo per sviluppare e produrre prodotti con tempi di sviluppo e realizzazione inimmaginabili per tecnologie di produzione tradizionale. Inoltre la stampa 3D può garantire continuità produttiva anche in momenti critici come questo in cui si interrompe la normale catena di approvvigionamento.
Ieri sera parlavo con Sergio Angelini che mi ha confidato che queste sono state fra le settimane più intense e belle della sua vita e dal punto di vista di relazioni umane ha raccolto un sacco di energie positive. Non posso che concordare con lui.”