Oggi nel mercato manifatturiero, la sfida più impegnativa per progettisti, produttori, costruttori di linee e system integrators è quella di passare dalle idee alla pratica in modo rapido ed efficiente. L’obiettivo è quello di adottare tutte le misure possibili per agevolare l’innovazione ed evitare inutili ritardi e rielaborazioni.
Del resto, per tutti il tempo è denaro.
Per rimanere competitive, le aziende manifatturiere devono quindi ottimizzare tutti i loro processi, dall’architettura e dall’ingegneria del prodotto, fino all’installazione e alla messa in opera dello stesso, il tutto rivolgendo un’attenzione particolare all’area che spesso rappresenta la sfida più grande: il commissioning (letteralmente “messa in servizio”).
Le attuali esigenze di mercato spingono verso la richiesta di macchine e impianti custom che spesso non sono più ordinabili da un catalogo di prodotti standard, perché le specifiche degli impianti e dei prodotti sono personalizzate di volta in volta e vengono inserite in un progetto che viene discusso e ottimizzato, per ottenere una soluzione su misura concordata tra cliente e fornitore.
In questi tipi di contesto, il commissioning tradizionale presenta rischi considerevoli sia per i clienti, sia per i fornitori, perché le operazioni di verifica vengono svolte direttamente sul campo, avvalendosi solitamente di prototipi o delle macchine stesse già in fase di realizzazione avanzata.
Cos’è il Commissioning?
Con Commissioning si intende il processo di verifica di un sistema progettato e installato prima che il sistema stesso venga effettivamente utilizzato, per capire se rispetti le specifiche di progetto e se sia idoneo allo scopo prefissato. Tradizionalmente, questo comporta un lavoro di collaudo svolto tipicamente in una officina.
In genere, la fase di commissioning occupa circa il 25% del tempo nel progetto di costruzione di una linea e può essere responsabile fino al 70% dei ritardi del progetto causati dalle conseguenze di errori di progettazione o nel software di controllo.
Questa sproporzione tra tempi di realizzazione e possibili ritardi può portare a costose rilavorazioni e può avere anche un impatto negativo sulla comunicazione e sul rapporto di fiducia tra cliente e fornitore.
Il Virtual Commissioning nasce quindi con l’ottica di ottimizzare la fase di commissioning e renderla più efficiente fin dall’inizio del processo minimizzando i possibili ritardi del progetto.
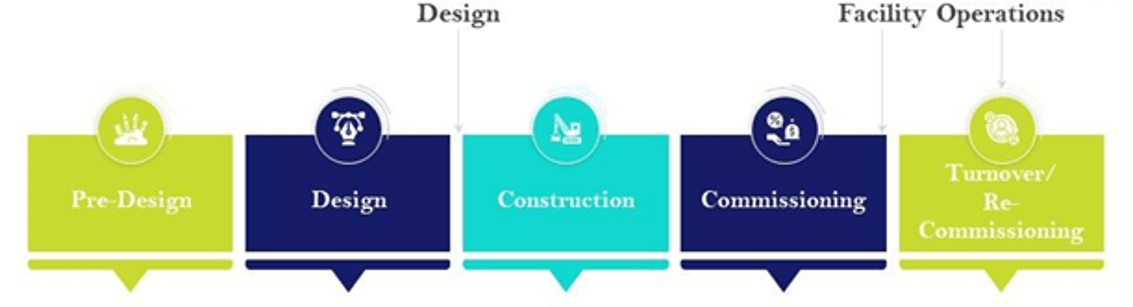
Cos’è il Virtual Commissioning?
Il Virtual Commissioning permette di eseguire i test di funzionamento di una macchina o di un impianto in un ambiente virtuale parziale o completo, migliorando la tradizionale messa in opera in officina e riducendo in modo significativo il rischio di costosi ritardi dovuti a errori e rilavorazioni.
Attraverso una simulazione software applicata al Digital Twin (o gemello digitale) è possibile far comunicare un modello virtuale con la macchina reale per riprodurne il comportamento in un ambiente virtuale e ottimizzarne le prestazioni prima di metterla realmente in funzione.
Gli attuali sistemi industriali, come ad esempio macchinari, transfer, impianti, sono sempre più automatizzati, includono spesso sofisticati strumenti, robot, linee di trasferimento ed equipaggiamenti di sicurezza e sono solitamente controllati da soluzioni programmabili (PLC, Motion Control, CNC).
Attraverso il Virtual Commissionig, è possibile interfacciarsi con questi sistemi e simulare la realizzazione di un impianto, mostrando il progetto ancora prima della sua realizzazione, oppure di simularne il funzionamento consentendo di effettuare modifiche in tempo reale e di ottimizzare le risorse in termini economici e produttivi.
Come funziona il Virtual Commissioning?
Il Virtual Commissioning può essere suddiviso in tre fasi principali: la modellazione, la simulazione e la validazione.
I tecnici che si occupano di automazione partono dal modello 3D della macchina da simulare e ne definiscono gli accoppiamenti con i relativi vincoli cinematici; tenendo conto poi delle condizioni al contorno, come ad esempio attriti e gravità, possono arrivare a simulare la realtà al 100%.
Successivamente, definiscono gli azionamenti, le fasi di funzionamento, le leggi di moto e infine vengono simulati i segnali di Input/Output. Definito così il digital twin della macchina da simulare, è possibile iniziare a effettuare tutti i test e a correggere eventuali errori di progettazione, di programmazione e di funzionamento, esattamente come accadrebbe in una situazione reale, ma senza attendere il tempo di produzione e montaggio di un prototipo.
Per questo motivo, il Virtual Commissioning può ridurre significativamente la durata del progetto legata principalmente ai tempi di inattività.
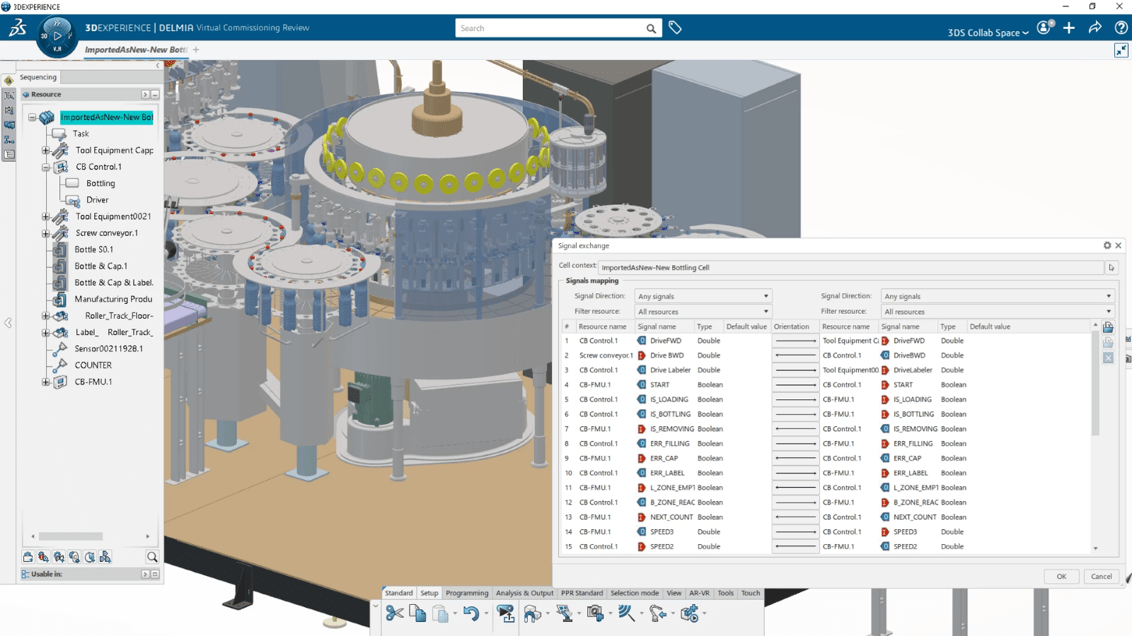
Quali sono i vantaggi del Virtual Commissioning?
Per come viene concepito e per come viene effettuato, il Virtual Commissioning porta indubbiamente numerosi benefici a chi decide di adottarlo. In particolare:
- consente di ottimizzare il progetto meccanico prima di realizzare qualsiasi componente
- consente di ridurre i tempi di sviluppo del software a corredo della macchina, favorendo la fase di debug senza la necessità di ricorrere ad un prototipo reale
- permette di analizzare l’efficienza di un impianto, migliorandone le prestazioni e anticipando eventuali malfunzionamenti
- permette lo studio dei percentili, per studiare il corretto bilanciamento delle attività umane e delle risorse e garantire inoltre la sicurezza durante il funzionamento dell’impianto
- agevola il supporto post-vendita perché consente di effettuare verifiche di primo livello, riducendo i costi di intervento e di manutenzione
- riduce sensibilmente i costi legati ai tempi di installazione, di controllo e di ottimizzazione dell’impianto
- aumenta la qualità dei prodotti, perché l’impianto nasce già praticamente collaudato.
Conclusioni
Il nuovo approccio, basato sul Virtual Commissioning presenta indiscutibili vantaggi, come ad esempio il risparmio di tempo, la riduzione dello stress al momento del “Go-Live” e una migliore qualità dei progetti e dei prodotti. Per poter mettere in pratica il Virtual Commissioning servono però soluzioni potenti e innovative, che possano garantire la gestione e la simulazione di tutti gli scenari realistici.
I ruoli del brand DELMIA, basati sulla Piattaforma 3DEXPERIENCE, offrono alle aziende il modo migliore e ottimale per progettare e testare le linee, perché permettono ai progettisti di lavorare con gli strumenti che conoscono, fornendo un ambiente sicuro per la comunicazione, la collaborazione e la continuità digitale. La perfetta integrazione del sistema consente a tutte le parti interessate di accedere ai progetti più recenti, proteggendo al contempo la proprietà intellettuale di chi contribuisce al progetto.
Contattaci per ulteriori informazioni o per avere maggiori approfondimenti.